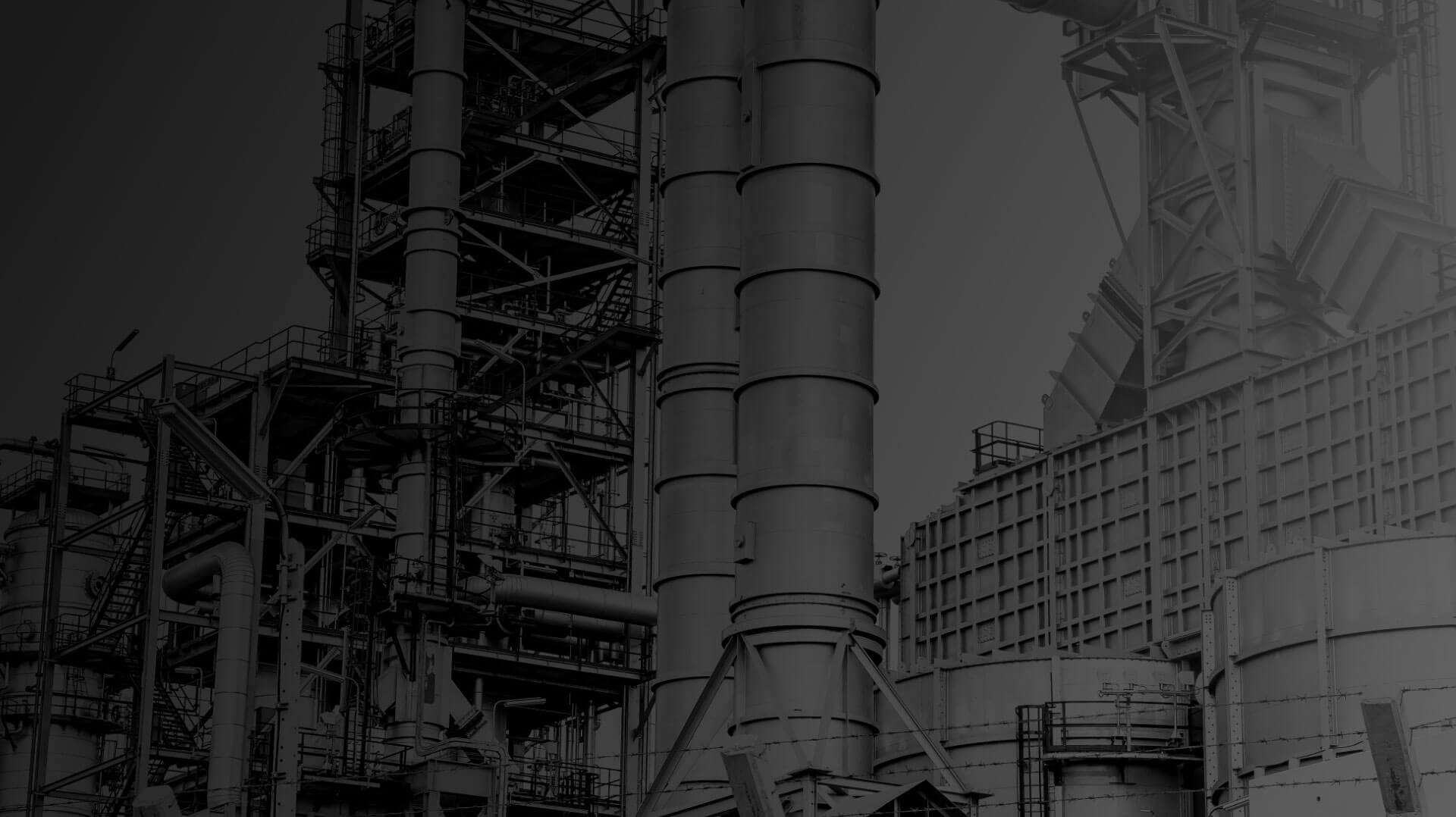
ENERGY & INDUSTRIAL
MAXIMIZE
EQUIPMENT UPTIME
AND ELIMINATE
UNSCHEDULED
MAINTENANCE
Gastops critical component intelligence helps operators of wind turbines, gas turbines, aeroderivative engines and other rotating equipment:
Eliminate unplanned downtime
Eliminate secondary damage
Eliminate unplanned repair and assessment costs
Predict Remaining Useful Life (RUL) of equipment
Quickly evaluate equipment health for large fleets
Enable predictive maintenance at scale
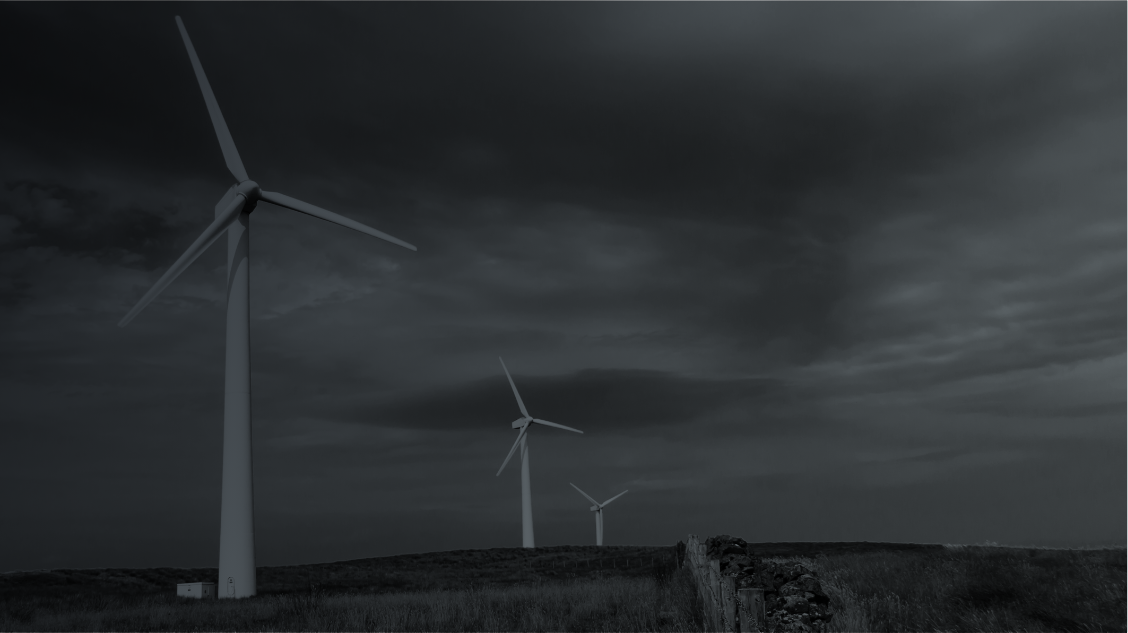
Wind Turbine Operators and Manufacturers
Gastops offers real-time operating costs savings through its critical component intelligence. Gastops reduces operating risk and provides a real-time view into wind farm operations, lowering the cost of wind energy production.
LEARN MORE 
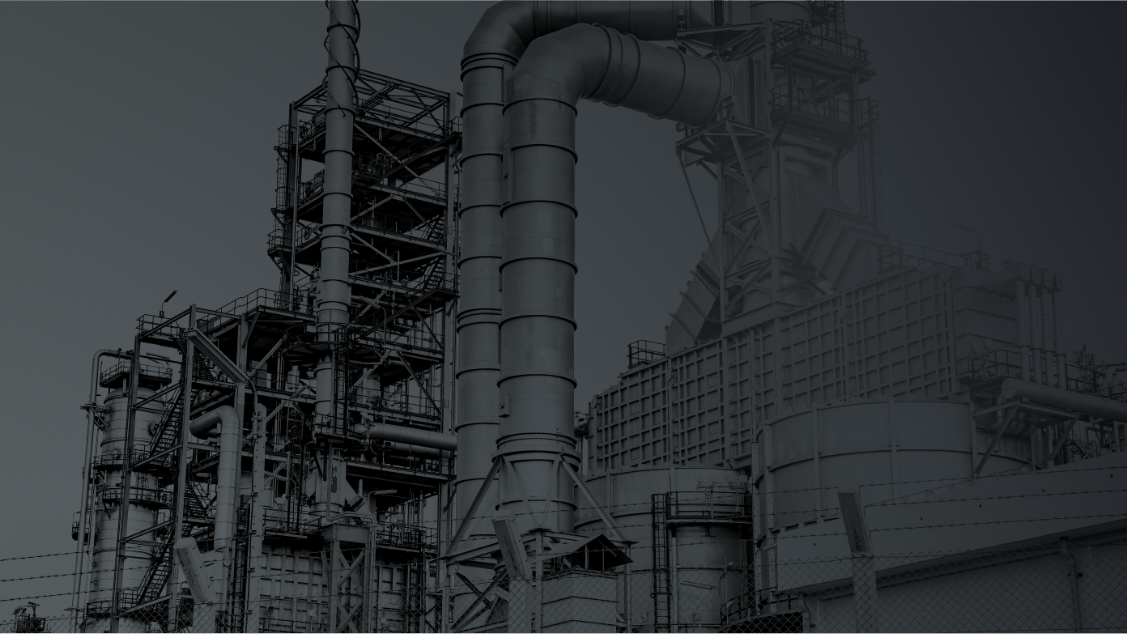
Predictable logistics and no unplanned events. Gastops offers the industry’s earliest warning of impending equipment failure and real-time monitoring of damage progression, enabling operators to make the best maintenance decisions.
LEARN MORE 
Aeroderivative Gas Turbine Operators and Manufacturers
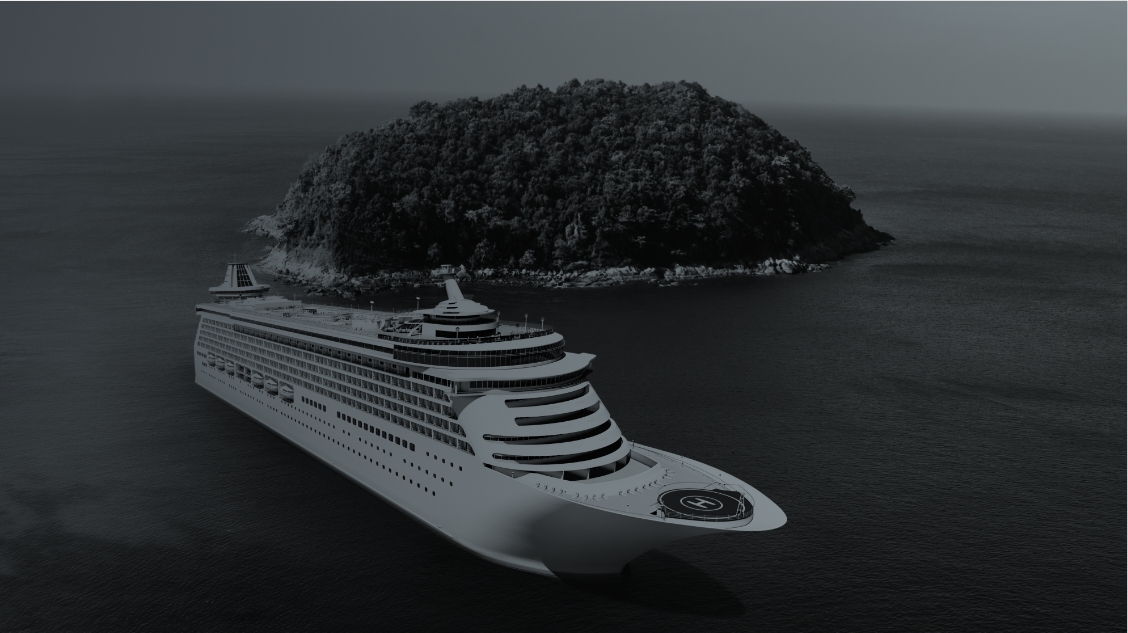
Operators of Cruise Ship and FPSO Fleets
Optimized propulsion system health through real-time monitoring and advanced dynamic simulation. Gastops offers ship operators real-time health monitoring of critical rotating equipment as well as a fully-functional virtual model for testing propulsion and other vessel systems.
LEARN MORE 
Discover
the future of equipment condition intelligence.
Talk to one
of our experts today.